Takım tezgahları dünyasında, proseslerin optimum tasarımı en yüksek hassasiyet ve verimliliğe ulaşmak için hayati önem taşıyor. EMAG Koepfer Teknoloji ve Ürün Yönetimi Başkanı ve Yönetim Kurulu Üyesi Jörg Lohmann, azdırma işlemlerinin nasıl tasarlandığı hakkında planet dişlileri örnek olarak kullanıyor. Dişli azdırma makineleri ve dişli kesme işlemlerinin tasarımı ve uygulamasında yaklaşık 20 yıllık deneyime sahip olan Jörg Lohmann, EMAG tarafından şirket içi gerçekleştirilen röportajda, bu işlemlerin arkasındaki karar verme süreçlerine dair açıklamalarda bulunuyor.
EMAG Koepfer’i özel kılan nedir?
Buna cevap vermek o kadar kolay değil. EMAG Koepfer, herkesin temelde birbirini tanıdığı resmi olmayan bir şirkettir. Meslektaşlar arası iş birliği, profesyonel yetkinlik ve deneyimin birleşimi, bunca yıldan sonra hala işe gitmekten keyif alıyor olmama katkıda bulunuyor. Sanırım müşterilerimiz de bunu hissediyor. Her proje için bireysel ve yetkin danışmanlık hizmetleri ve destek alıyorlar ve endişelerinin ciddiye alınacağına güvenebiliyorlar. EMAG Grubu ile olan bağlantımız sayesinde, örneğin karmaşık üretim süreçlerinin uygulanmasından anahtar teslim üretim sistemlerine kadar müşteri taleplerine çok bireysel olarak yanıt verebiliyoruz. Bu nedenle EMAG Koepfer, kişisel iletişim, uzmanlık ve zengin deneyimin benzersiz bir karışımını sunuyor. Bunların hepsi de şirketi ve çözümlerimizi çok özel kılıyor.
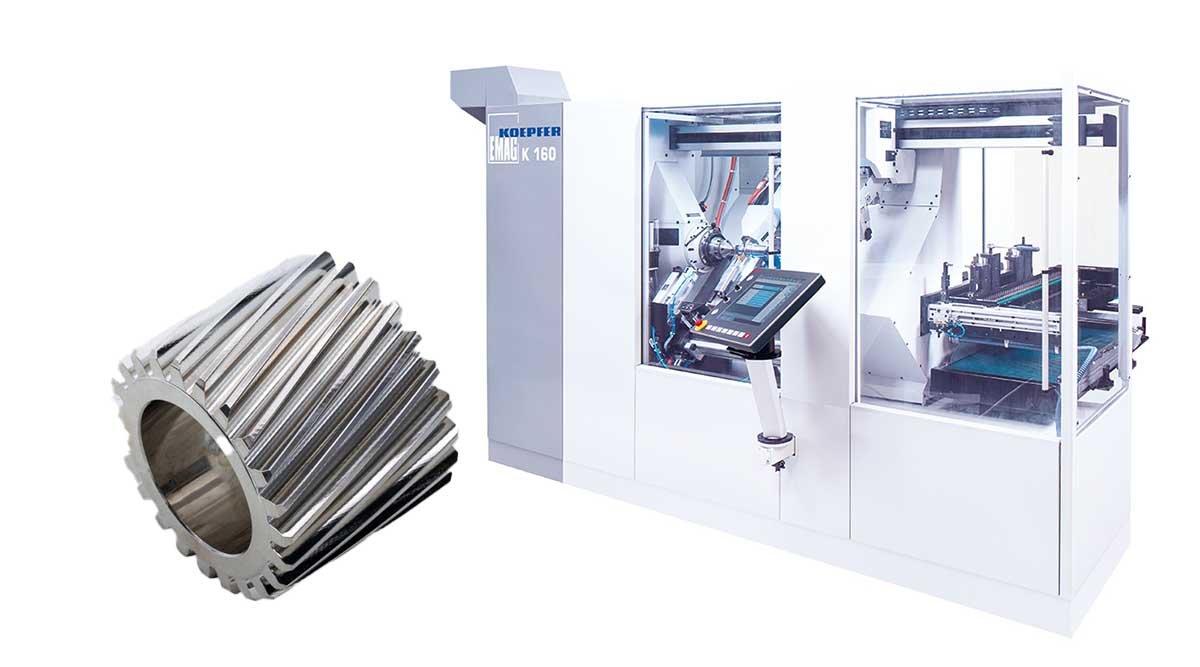
Deneyim azdırma proseslerinin tasarımı için de önemli. Burada tam olarak nasıl ilerliyorsunuz?
Evet, deneyim çok önemli ancak öncelikle bu karmaşık teknolojinin fiziksel ve teknik yönlerini tam olarak anlamanız ve bunlara nüfuz etmeniz gerekiyor. Bu, işleme süreçleri alanındaki genel bilgi birikimiyle desteklenen derin bir matematiksel anlayış gerektirir. EMAG Koepfer’de durum böyleyse, daha da ileri giderek dişli kesme süreçlerinin geliştirilmesinde en önemli kaynağın deneyim olduğunu söyleyebilirim. Ama şimdi kendimi aşıyorum. Tüm geliştirme sürecini biraz daha canlı bir şekilde anlatabilmek için bunu bir örnekle açıklamak istiyorum. Bir planet dişlisini düşünelim, burada büyük miktarlarda üretilmesi gereken nihai üründen yüksek talepler söz konusu.
Tasarım genellikle iş parçası çiziminin ve müşteriden gelen, yukarı ve aşağı süreçler için gereksinimler, dişli işleme sonrası kalite sınıfı, istenen miktarlar vb. gibi çerçeve koşullarını içeren spesifikasyon sayfasının alınmasıyla başlar. Bu bilgiler, ilk tasarımın temelini oluşturmanın yanı sıra, bir işleme sürecinin ilk taslaklarının da temelini oluşturur. Süreç tasarımı için sayısız olasılığın yanı sıra, dikkate alınması gereken çok sayıda faktör vardır. İşte tam da bu noktada deneyimimiz devreye giriyor; çünkü daha az etkili birçok süreci çok erken bir aşamada eleyebiliyoruz. Buna dayanarak, daha sonra bir varyant hesaplamasına girer ve en ekonomik çözümü belirlemek için farklı proses varyantlarını karşılaştırırsınız.
Kendinize soracağınız ilk soru nedir?
Her şeyden önce, bitmiş bileşenin neye benzemesi gerektiğini bilmeniz gerekir. Tüm süreç zinciri ve dişli işlemeye yönelik gereksinimler buradan türetilir. Daha sonra ıslak veya kuru işleme kullanıp kullanmadığımız gibi diğer hususlar dikkate alınır. Kuru işleme, özellikle büyük miktarlar için genellikle daha verimlidir. Daha yüksek kesme verileri elde edilebilir ve sertleştirme öncesi yıkama gibi işlemlerden tasarruf edilebilir. Bu şekilde, iş parçalarının taşınması ve teslim süreleri azaltılabilir. Kuru proses bu nedenle birçok avantaj sunar ancak aynı zamanda yüksek talepler de getirir. Bir yandan gerekli performans ve hassasiyete sahip doğru makineye ihtiyacınız vardır, diğer yandan da süreci mükemmel bir şekilde yürütebilmek için belirli sayıda parçaya ihtiyacınız vardır. İşte bu noktada, bu süreci mükemmelleştirmek için gerekli olan deneyim tekrar devreye giriyor. Neyse ki EMAG Koepfer olarak, dünya çapında sayısız makine tedarik ettiğimiz örnek iş parçamız “planeter dişliler” için de tüm bu gereksinimleri karşılıyoruz.
Peki ya takımlar? Burada nelere dikkat edilmesi gerekiyor?
Azdırma işleminde makinenin yanı sıra, azdırma kesicisinin tasarımı da belirleyici kriterdir. Yani azdırma kesicisinin tasarımı ve seçilen kesme verileri birbirini etkiler. Aşağıdaki sorular ortaya çıkmaktadır. Azdırma kesicisi ne tür bir malzemeden yapılmalıdır? Bir şaft frezesi mi yoksa bir delik frezesi mi seçmelisiniz? Freze çakısının diş sayısı vb. tüm bunlar da olası kesme verilerini ve ayrıca üretilen diş profillerinin kalitesini etkiler. Bu aslında bizi azdırma işleminin tasarımının derinliklerine götürür çünkü burada verilen her kararın sonuçta maliyetler üzerinde de bir etkisi vardır. Bir şaftlı azdırma ucu bir delikli azdırma ucundan daha pahalıdır ancak daha uzun olacak şekilde tasarlanabilir ve bu nedenle yeniden taşlanması gerekmeden önce daha fazla bileşen işleyebilir. İşleme süresi ve üretilen diş profillerinin kalitesi, kesme verilerine ve ocak kesicinin tasarımına bağlıdır. Dediğim gibi, burada temel olarak her şey birbirine bağlıdır ve bunu denemekten kaçış yoktur.
Bu deneme yanılma sürecini nasıl hayal edebilirsiniz?
Elbette farklı tasarımları gerçekte denemeyiz; ancak bu işlem adımı için simülasyon yazılımı kullanırız. Burada yine deneyime başvurmak zorundayım çünkü uzun yıllara dayanan süreç tasarımına bakabilir ve hangi değerlerle başlamanın mantıklı olduğunu zaten biliriz. Bundan sonra gelen her şey temelde optimum maliyet/kalite oranının aranmasıdır. Başka bir deyişle, gerekli miktarları istenen kalitede en düşük birim üretim maliyetleriyle üretebileceğimiz işleme sürecini ararız. Bu da optimum işleme sürecidir. Örneğimizde bu, en azından yumuşak işleme söz konusu olduğunda, planet dişlilerini 9 saniyeden daha kısa sürede işleyebileceğimiz anlamına gelir. Planet dişliler önce frezelenir, ardından sertleştirilir ve daha sonra sert-ince işlenir. Ancak bu konuyu daha ayrıntılı olarak ele almak bu röportajın kapsamını aşacaktır. Bu nedenle, sizi tüm süreci ayrıntılı olarak açıkladığım web seminerimize davet etmek istiyorum.
