1.Mikro dişlilerde flank sapmaları
Mikro dişliler, özellikle tıbbi cihazlar, havacılık ve robotik gibi hassasiyet gerektiren alanlarda kullanılır ve yüksek hassasiyetle üretilmeleri gerekir. ANSI/AGMA ISO 1328-1 standardına göre, flank sapmaları (profil ve helis sapmaları) dikkatle kontrol edilmelidir. Bu sapmalar, dişlinin performansını doğrudan etkileyebilir, bu yüzden mikro dişlilerde ölçümler son derece önemlidir.
2.Profil sapmaları (Mikro dişliler için geçerli)
Profil Sapması (Fα), bir dişlinin gerçek flank yüzeyinin, tasarlanan involüt profile göre gösterdiği toplam sapmayı ifade eder.
Profil Eğim Sapması (fHα) ve Profil Form Sapması (ffα), mikro dişlilerde diş profilinin tasarımla ne kadar uyumlu olduğunu gösterir. Mikro dişlilerde küçük sapmalar bile büyük etkilere neden olabilir.
Toplam Profil Toleransı (FαT), eğim ve form sapmalarının birleşimi ile hesaplanır ve şu formülle bulunur:
3.Mikro dişlilerde helis sapmaları
.
Helis sapmaları, dişlilerin düzgün şekilde etkileşimde bulunmasını sağlar. Mikro dişlilerde, Helis Eğim Sapması (fHβ) ve Helis Form Sapması (ffβ) dikkatle kontrol edilmelidir. Dişlinin yüzey genişliği boyunca tasarlanmış helis yörüngesinden sapmalar, sistem performansını olumsuz etkileyebilir.
4.Tolerans sınıfları ve mikro dişli üretimi
ANSI/AGMA ISO 1328-1 standardı, 1’den (en hassas) 11’e kadar değişen 11 tolerans sınıfını tanımlar. Mikro dişlilerde, daha yüksek hassasiyet sınıfları (örn. 3 veya 4) tercih edilir. Yüksek hassasiyetli mikro dişliler, genellikle yüksek doğruluk ve düşük sapma toleranslarına sahip olmalıdır.
5.Mikro dişliler için flank sapma ölçüm tablosu
ANSI/AGMA ISO 1328-1 standardına göre mikro dişlilerde kullanılan normal modül (mn) aralıkları için flank sapma değerleri aşağıdaki tabloda verilmiştir. Modül 0,1 mm’den başlayarak 1,0 mm’ye kadar artan sapma değerleri sunulmuştur:
Bu tabloda verilen değerler,
Normal Modül (mn) | Profil Sapması (FaT) | Helis Sapması (FβT) | Tek Diş Sapması (fpT) | Toplam Sapma (FpT) |
---|---|---|---|---|
0.1 | 1.2 µm | 1.4 µm | 1.0 µm | 1.5 µm |
0.2 | 1.5 µm | 1.6 µm | 1.2 µm | 1.8 µm |
0.3 | 1.8 µm | 1.9 µm | 1.5 µm | 2.1 µm |
0.4 | 2.0 µm | 2.2 µm | 1.7 µm | 2.4 µm |
0.5 | 2.2 µm | 2.5 µm | 1.9 µm | 2.7 µm |
0.6 | 2.5 µm | 2.7 µm | 2.1 µm | 3.0 µm |
0.7 | 2.8 µm | 3.0 µm | 2.3 µm | 3.4 µm |
0.8 | 3.0 µm | 3.3 µm | 2.5 µm | 3.7 µm |
0.9 | 3.2 µm | 3.5 µm | 2.7 µm | 4.0 µm |
1.0 | 3.5 µm | 3.8 µm | 3.0 µm | 4.3 µm |
mikro dişlilerde yüksek hassasiyet gereksinimlerini karşılamak için uyarlanmıştır. Bu sapma toleransları, dişlilerin çalışma performansını sağlamak için gerekli olan maksimum sapma sınırlarını göstermektedir.
6.Çift flank testinin tanımı ve işlevi
Çift flank testi, dişli sistemlerinde kaliteyi sağlamak ve yüzey uyumunu değerlendirmek amacıyla yaygın olarak kullanılan bir test yöntemidir. Bu test, mastar dişli ile test edilecek dişlinin eksenel olarak sıkı temasta tutulduğu bir düzenekte gerçekleştirilir. Diş yüzeyleri arasındaki temas anında eksenel mesafedeki değişimler, dişlinin yüzey kalitesi, hizalanma doğruluğu ve sistemdeki uyum hakkında ayrıntılı bilgi sunar. Test sırasında mastar dişli, teorik olarak hatasız kabul edilirken, test edilen dişlinin performansını değerlendirmek için referans olarak kullanılır. Çift flank testi, özellikle dişliler arasındaki montaj hatalarının, diş yüzeyindeki kusurların ve sapmaların erken aşamada tespit edilmesini sağlar ve bu sayede daha büyük arızaların önüne geçer.
Bu test yöntemi hem büyük dişli sistemlerinde hem de mikro dişlilerde uygulanabilir. Ancak mikro dişlilerde test süreci daha fazla hassasiyet gerektirir; çünkü bu tür sistemlerde milimetrenin altındaki sapmalar bile performansı ciddi şekilde etkileyebilir. Çift flank testinin en büyük avantajı, her iki diş yüzeyini aynı anda analiz edebilmesidir. Diş profilleri arasındaki temasın kesintisiz sağlanması, tüm çalışma aralığı boyunca eksenel mesafe değişimlerinin ölçülmesine olanak tanır. Böylece, test edilen dişlinin montaj doğruluğu, yüzey pürüzlülüğü ve çalışma koşullarında göstereceği performans gerçekçi bir şekilde değerlendirilir.
Test sırasında ölçülen temel parametrelerden biri, Radyal Bileşik Sapma (Fpi) olarak adlandırılır. Bu parametre, test boyunca ölçülen en büyük ve en küçük eksenel mesafe arasındaki farkı ifade eder. Fpi = max(Fpi) – min(Fpi).
Bireysel Tek Adım Sapması (Fpi):
Fpi, her bir dişlinin ölçüm çapındaki teorik adım ile gerçek adım arasındaki cebirsel farkı ifade eder. Bu fark, bir dişin teorik pozisyonuna kıyasla, bitişik dişin yer değiştirmesini temsil eder. Dişlilerin sol ve sağ yüzeyleri için diş sayısı kadar Fpi değeri bulunur. Fpi, bir sektördeki bitişik adımların toplam bireysel adım sapmalarının cebirsel toplamına eşittir. Yani, her bir dişten alınan sapma değeri, dişlilerin teorik yerleşimi ile gerçek yerleşimi arasındaki farkı gösterir .
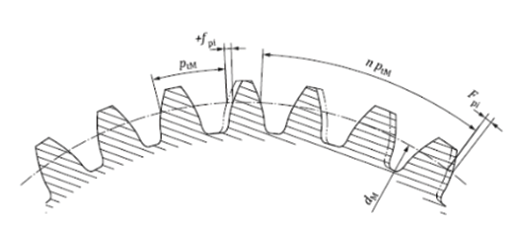
Bireysel Bitişik Adım Farkı (Fui):
Fui, iki ardışık bireysel adımın gerçek ölçülen değerleri arasındaki farkı ifade eder. Başka bir deyişle; Fui, iki ardışık adımın bireysel tek adım sapmalarının farkıdır. İki ardışık diş arasındaki farkın maksimum değeri olarak tanımlanır. Bu değer, dişli sistemlerinin düzgün çalışıp çalışmadığı hakkında önemli bilgiler sunar. Fpi değeri, dişlinin eksenel düzlemde gösterdiği doğruluk ve uyumun göstergesidir. Bunun yanı sıra, dişten dişe sapma (Fpi) ise ardışık iki dişin temas sırasında oluşturduğu eksenel farkı tanımlar. Bu parametreleri birlikte incelenerek, sistemin genel performansı hakkında kapsamlı bir değerlendirme yapılır. Veriler, özellikle şanzıman dişlileri gibi yüksek hassasiyet gerektiren uygulamalarda kritik öneme sahiptir.
Çift flank testinin sağladığı bir diğer önemli avantaj, dişlilerin çalışırken karşılaşabileceği gürültü ve titreşim sorunlarının önceden tespit edilmesidir. Dişliler arasındaki eksenel mesafe değişimleri, sistemin çalışma sırasında oluşturabileceği mekanik titreşimlerin kaynağını gösterebilir. Bu tür titreşimler zamanla diş yüzeylerinde aşınmaya neden olabilir ve sistemin genel ömrünü kısaltabilir. Çift flank testi sayesinde, bu tür sorunlar henüz üretim aşamasında belirlenir ve gerekli düzeltici işlemler yapılabilir.
Mikro dişli sistemlerinde, test süreçleri daha karmaşık ve zorlayıcıdır. Dişlilerin küçük boyutları, ölçüm cihazlarının çözünürlüğünün yüksek olmasını gerektirir. Mikro ölçekte çift flank testi yaparken, ölçüm cihazlarının nanometre seviyesinde doğruluğa sahip olması kritik öneme sahiptir. Bu nedenle, mikro dişliler için çift flank testi genellikle temassız optik sensörlerle desteklenir. Kromatik konfonkal sensörler ve lazer interferometreler gibi sistemler, yüzeyde temas olmadan ölçüm yaparak hem doğruluğu artırır hem de diş yüzeyinde oluşabilecek hasarları önler.
Test sırasında elde edilen sapmaların analizinde Fourier dönüşümü gibi matematiksel teknikler kullanılır. Bu dönüşüm, sistemden gelen gürültüyü filtreleyerek, net ve doğru sonuçlar elde edilmesini sağlar. İki noktalı hata ayrımı yöntemi, test verilerinden oluşan kurulum sapmalarını ayrıştırır.
Elde edilen bu veriler, dişlilerin çalışma performansını ve montaj doğruluğunu analiz etmek için kullanılır. Eksenel mesafe değişimlerinden elde edilen grafikler, dişlilerin gürültü ve titreşim potansiyelini önceden tespit etmeye olanak tanır.
Bu testin doğruluğunu artırmak için dişlilerin üretimi sırasında ISO 1328-1 ve AGMA 2015-1-A01 gibi standartlar uygulanır. Ayrıca, diş profilleri DIN 3960-3962 standartlarına göre değerlendirilir. Bu standartlara uyum, test süreçlerinin uluslararası kabul görmesini sağlar.
Sonuç olarak, çift flank testi, dişli sistemlerinde kalite kontrol, hata tespiti ve performans değerlendirmesi açısından hayati bir araçtır. Mikro dişlilerde bu testin önemi daha da artmakta, çünkü küçük sapmaların bile sistem performansı üzerinde büyük etkileri olabilmektedir. Standartlara uygun şekilde yürütülen çift flank testleri, üretim hattında kaliteyi güvence altına alırken, dişli sistemlerinin kullanım ömrünü uzatır ve müşteri memnuniyetini artırır. Bu veya benzeri güç aktarım grubu ile ilgili tüm sorularınız için temasa geçebilirsiniz.
Referanslar:
[1] ANSI/AGMA ISO 1328-1:2013, Cylindrical Gears – ISO System of Accuracy – Part 1: Definitions and Allowable Values of Deviations Relevant to Corresponding Flanks of Gear Teeth, American National Standards Institute, 2013.
[2] DIN 3960-3962, Gear Technology – Basic Terms and Calculation Methods for Gears, Deutsches Institut für Normung, 1989.
[3] Müller, R., and Fischer, P., High-Precision Gear Measurement for Micro Gears Using Optical and Tactile Methods, Journal of Mechanical Engineering, vol. 45, no. 2, 2020, pp. 135-142.
[4] Zhang, J., and Liu, Z., Analysis of Profile and Helix Deviations in Micro Gears, International Journal of Precision Engineering and Manufacturing, vol. 18, no. 3, 2019, pp. 267-275.